Destylator przemysłowy to urządzenie, które odgrywa kluczową rolę w procesach separacji cieczy na podstawie różnic w ich temperaturach wrzenia. W praktyce oznacza to, że destylacja pozwala na wydobycie czystych składników z mieszanin, co jest niezbędne w wielu gałęziach przemysłu, takich jak chemiczny, farmaceutyczny czy petrochemiczny. Proces ten zazwyczaj rozpoczyna się od podgrzewania cieczy, co powoduje jej parowanie. Opary następnie są kierowane do kondensatora, gdzie schładzają się i skraplają, tworząc czystą frakcję. W zależności od zastosowania, destylatory mogą być zaprojektowane do pracy w różnych warunkach ciśnienia i temperatury, co wpływa na efektywność procesu. W przemyśle chemicznym destylatory są często wykorzystywane do produkcji rozpuszczalników oraz innych substancji chemicznych, które muszą być wysokiej czystości.
Jakie są rodzaje destylatorów przemysłowych i ich zastosowania
W przemyśle istnieje wiele różnych typów destylatorów, które różnią się zarówno konstrukcją, jak i zastosowaniem. Najpopularniejsze z nich to destylatory prostokątne oraz kolumnowe. Destylatory prostokątne są najczęściej stosowane w procesach o dużej skali produkcji, gdzie wymagana jest wysoka wydajność. Z kolei destylatory kolumnowe charakteryzują się bardziej skomplikowaną budową i są używane głównie w procesach wymagających wielokrotnej separacji składników. Innym rodzajem są destylatory próżniowe, które działają w obniżonym ciśnieniu, co pozwala na destylację substancji o wysokich temperaturach wrzenia bez ryzyka ich rozkładu. W przemyśle petrochemicznym wykorzystuje się również destylatory frakcyjne do oddzielania różnych frakcji ropy naftowej.
Jakie materiały są wykorzystywane do budowy destylatorów przemysłowych
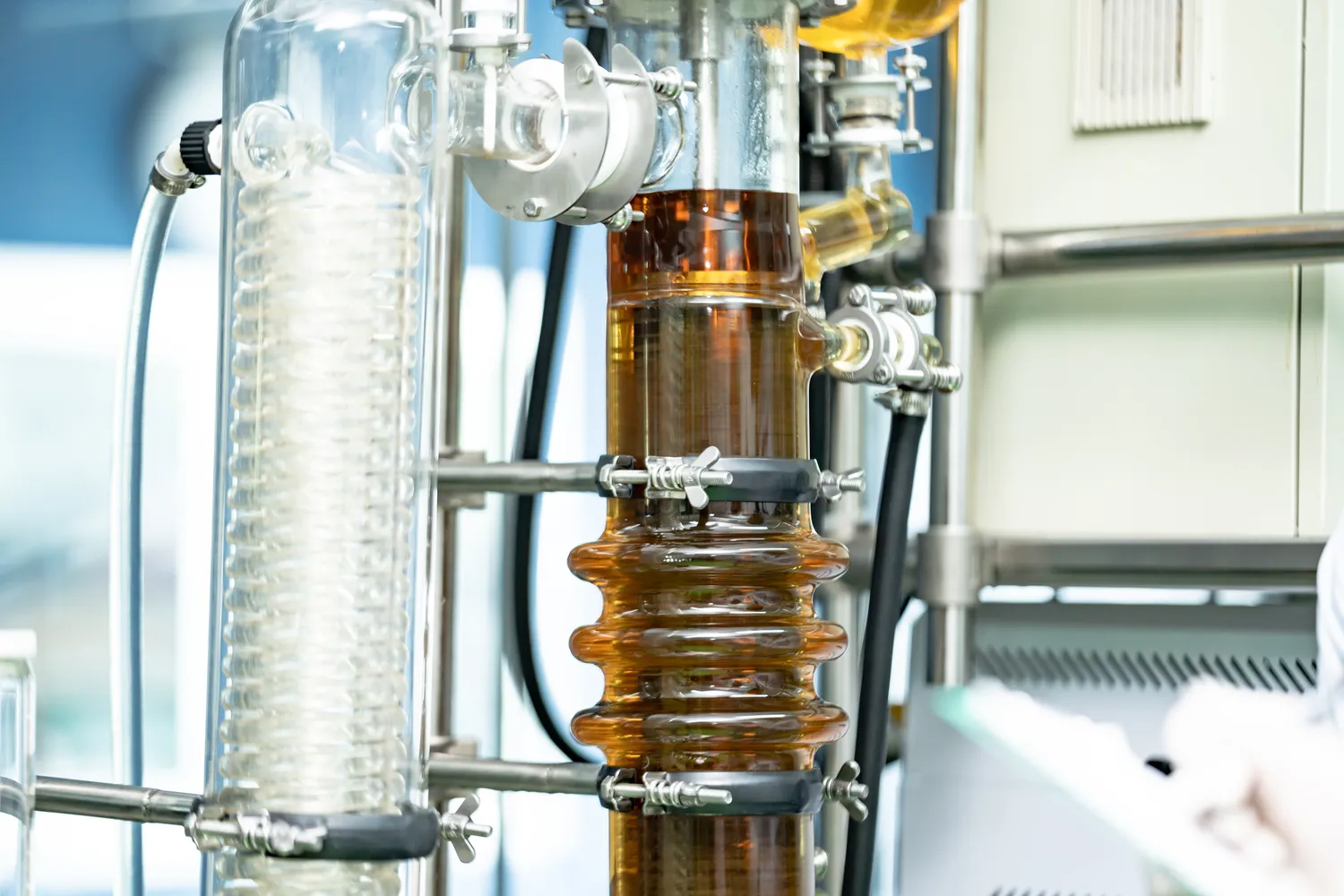
Destylator przemysłowy
Budowa destylatorów przemysłowych wymaga zastosowania materiałów odpornych na wysokie temperatury oraz korozję chemiczną. Najczęściej stosowanym materiałem jest stal nierdzewna, która zapewnia trwałość oraz odporność na działanie agresywnych substancji chemicznych. W przypadku bardziej wymagających aplikacji można również spotkać destylatory wykonane z materiałów takich jak tytan czy szkło borokrzemowe. Szkło jest szczególnie cenione w laboratoriach ze względu na swoją neutralność chemiczną oraz możliwość obserwacji procesów zachodzących wewnątrz urządzenia. Dodatkowo elementy takie jak uszczelki muszą być wykonane z materiałów odpornych na wysoką temperaturę oraz działanie chemikaliów, aby zapewnić szczelność systemu.
Jakie są zalety stosowania destylatorów przemysłowych w produkcji
Stosowanie destylatorów przemysłowych przynosi wiele korzyści dla producentów w różnych branżach. Przede wszystkim umożliwia uzyskanie wysokiej czystości produktów końcowych, co jest kluczowe w takich sektorach jak farmaceutyka czy chemia. Dzięki precyzyjnemu procesowi separacji możliwe jest wydobycie pożądanych składników przy minimalnych stratach surowców. Ponadto nowoczesne technologie stosowane w destylatorach pozwalają na automatyzację procesów, co zwiększa efektywność produkcji oraz redukuje koszty operacyjne. Kolejną zaletą jest możliwość dostosowania parametrów pracy urządzenia do specyfiki danej produkcji, co pozwala na optymalizację procesu i lepsze wykorzystanie dostępnych zasobów.
Jakie wyzwania stoją przed producentami destylatorów przemysłowych
Producenci destylatorów przemysłowych stają przed wieloma wyzwaniami związanymi z rosnącymi wymaganiami rynku oraz postępem technologicznym. Jednym z głównych problemów jest konieczność ciągłego doskonalenia technologii produkcji, aby sprostać oczekiwaniom klientów dotyczących efektywności i jakości produktów. W miarę jak przepisy dotyczące ochrony środowiska stają się coraz bardziej rygorystyczne, producenci muszą także zwracać uwagę na aspekty ekologiczne swoich urządzeń, takie jak zużycie energii czy emisja zanieczyszczeń. Kolejnym wyzwaniem jest potrzeba dostosowywania oferty do różnorodnych potrzeb klientów z różnych branż, co wymaga elastyczności i innowacyjności w projektowaniu nowych rozwiązań.
Jakie są najnowsze trendy w technologii destylacji przemysłowej
W ostatnich latach technologia destylacji przemysłowej przechodzi dynamiczne zmiany, które mają na celu zwiększenie efektywności procesów oraz minimalizację wpływu na środowisko. Jednym z najważniejszych trendów jest rozwój systemów automatyzacji i monitorowania, które pozwalają na zdalne zarządzanie procesami destylacji. Dzięki zastosowaniu zaawansowanych czujników i oprogramowania, operatorzy mogą na bieżąco śledzić parametry pracy urządzenia, co umożliwia szybką reakcję na ewentualne problemy. Kolejnym istotnym kierunkiem rozwoju jest integracja technologii destylacji z odnawialnymi źródłami energii, co przyczynia się do obniżenia kosztów operacyjnych oraz zmniejszenia emisji gazów cieplarnianych. Wiele firm inwestuje także w badania nad nowymi materiałami, które mogą poprawić wydajność i trwałość destylatorów.
Jakie są kluczowe czynniki wpływające na efektywność destylatorów przemysłowych
Efektywność destylatorów przemysłowych zależy od wielu czynników, które mogą znacząco wpłynąć na jakość i ilość uzyskiwanych produktów. Jednym z najważniejszych elementów jest temperatura podgrzewania cieczy, która musi być precyzyjnie kontrolowana, aby zapewnić optymalne warunki do parowania i skraplania. Również ciśnienie w systemie ma kluczowe znaczenie – w niektórych przypadkach obniżenie ciśnienia może prowadzić do zwiększenia wydajności procesu. Kolejnym czynnikiem jest konstrukcja samego destylatora; różne typy kolumn czy wymienników ciepła mogą mieć różny wpływ na efektywność separacji składników. Ważne jest także odpowiednie dobranie materiałów budowlanych, które muszą być odporne na działanie chemikaliów oraz wysokie temperatury. Nie można zapominać o regularnej konserwacji urządzeń, która ma kluczowe znaczenie dla ich długotrwałej i bezawaryjnej pracy.
Jakie są zastosowania destylatorów przemysłowych w różnych branżach
Destylatory przemysłowe znajdują szerokie zastosowanie w wielu branżach, co czyni je niezwykle wszechstronnymi urządzeniami. W przemyśle chemicznym są one wykorzystywane do produkcji różnorodnych substancji chemicznych, takich jak rozpuszczalniki, kwasy czy alkohole. W branży farmaceutycznej destylacja odgrywa kluczową rolę w procesach oczyszczania substancji czynnych oraz produkcji leków o wysokiej czystości. W przemyśle petrochemicznym destylatory frakcyjne służą do oddzielania różnych frakcji ropy naftowej, co jest niezbędne do produkcji paliw oraz innych produktów naftowych. Również w przemyśle spożywczym destylacja znajduje zastosowanie – przykładem mogą być procesy produkcji alkoholi takich jak whisky czy wódka, gdzie kluczowe jest uzyskanie odpowiedniej jakości trunku poprzez separację niepożądanych składników.
Jakie są koszty związane z zakupem i eksploatacją destylatorów przemysłowych
Koszty związane z zakupem i eksploatacją destylatorów przemysłowych mogą się znacznie różnić w zależności od wielu czynników, takich jak typ urządzenia, jego wielkość oraz specyfika zastosowania. Inwestycja w nowoczesny destylator może być znaczna, jednak warto pamiętać, że długoterminowe oszczędności wynikające z efektywności energetycznej oraz zmniejszenia strat surowców mogą szybko zrekompensować początkowe wydatki. Koszty eksploatacyjne obejmują nie tylko zużycie energii elektrycznej czy paliwa potrzebnego do podgrzewania cieczy, ale także regularną konserwację oraz ewentualne naprawy urządzenia. Warto również uwzględnić koszty związane z zatrudnieniem wykwalifikowanego personelu obsługującego urządzenie oraz szkoleniem pracowników. W przypadku dużych zakładów przemysłowych istotnym elementem kosztów może być także przestrzeń potrzebna do instalacji urządzeń oraz ich integracji z innymi systemami produkcyjnymi.
Jakie są regulacje prawne dotyczące stosowania destylatorów przemysłowych
Stosowanie destylatorów przemysłowych wiąże się z koniecznością przestrzegania licznych regulacji prawnych dotyczących ochrony środowiska oraz bezpieczeństwa pracy. W wielu krajach istnieją przepisy regulujące emisję substancji szkodliwych do atmosfery oraz wymagania dotyczące gospodarki odpadami powstałymi podczas procesów destylacyjnych. Przemysł chemiczny i farmaceutyczny często podlega szczegółowym normom dotyczącym jakości produktów końcowych oraz ich wpływu na zdrowie ludzi i środowisko naturalne. Dlatego przedsiębiorstwa muszą regularnie przeprowadzać audyty zgodności z obowiązującymi przepisami oraz wdrażać odpowiednie procedury kontrolne. Ponadto wiele krajów wymaga uzyskania specjalnych zezwoleń na prowadzenie działalności związanej z produkcją substancji chemicznych czy alkoholi, co wiąże się z dodatkowymi formalnościami administracyjnymi.
Jakie są przyszłościowe kierunki rozwoju technologii destylacji przemysłowej
Przyszłość technologii destylacji przemysłowej zapowiada się obiecująco dzięki ciągłemu postępowi technologicznemu oraz rosnącemu naciskowi na zrównoważony rozwój. W miarę jak coraz więcej firm stawia na ekologię i efektywność energetyczną, możemy spodziewać się dalszego rozwoju systemów opartych na odnawialnych źródłach energii oraz innowacyjnych metodach recyklingu odpadów powstałych podczas procesów destylacyjnych. Technologia cyfrowa również będzie miała kluczowe znaczenie – rozwój sztucznej inteligencji i analizy danych pozwoli na jeszcze lepsze monitorowanie i optymalizację procesów produkcyjnych. Możliwe jest także pojawienie się nowych materiałów budowlanych o lepszych właściwościach termicznych i chemicznych, co wpłynie na wydajność i trwałość urządzeń. W przyszłości możemy również zobaczyć większe zainteresowanie miniaturyzacją technologii destylacyjnej, co umożliwi jej zastosowanie w mniejszych zakładach czy laboratoriach badawczych.