Destylarki do rozpuszczalników to urządzenia, które odgrywają kluczową rolę w procesach chemicznych, szczególnie w laboratoriach oraz przemyśle. Ich głównym celem jest oddzielanie różnych substancji na podstawie różnic w temperaturze wrzenia. Proces destylacji polega na podgrzewaniu cieczy, co powoduje jej parowanie, a następnie skraplaniu pary w celu uzyskania czystego rozpuszczalnika. W przypadku destylarek do rozpuszczalników, najczęściej używane są materiały odporne na działanie chemikaliów, co zapewnia ich długotrwałe użytkowanie. Warto również zauważyć, że istnieją różne typy destylarek, takie jak destylarki prostokątne czy kolumnowe, które różnią się konstrukcją i zastosowaniem. W laboratoriach często stosuje się także destylację frakcyjną, która pozwala na oddzielenie kilku składników jednocześnie. Dzięki temu można uzyskać wysokiej czystości substancje chemiczne, co jest niezwykle istotne w wielu dziedzinach nauki i przemysłu.
Jakie są zalety korzystania z destylarek do rozpuszczalników
Korzystanie z destylarek do rozpuszczalników niesie ze sobą wiele korzyści, które są istotne zarówno w kontekście przemysłowym, jak i laboratoryjnym. Przede wszystkim umożliwiają one uzyskanie wysokiej czystości substancji chemicznych, co jest niezbędne w wielu procesach badawczych oraz produkcyjnych. Dzięki zastosowaniu odpowiednich technologii destylacji można skutecznie oddzielać różne składniki mieszanin, co pozwala na ich dalsze wykorzystanie lub analizę. Kolejną zaletą jest oszczędność czasu i zasobów – nowoczesne destylarki są zaprojektowane tak, aby działały szybko i efektywnie, co przekłada się na zwiększenie wydajności pracy. Dodatkowo wiele modeli wyposażonych jest w systemy automatyzacji, co ułatwia obsługę i minimalizuje ryzyko błędów ludzkich. Warto również wspomnieć o aspektach ekologicznych – dzięki możliwości recyklingu rozpuszczalników można znacznie zmniejszyć ilość odpadów chemicznych generowanych podczas procesów produkcyjnych.
Jakie są najczęstsze zastosowania destylarek do rozpuszczalników
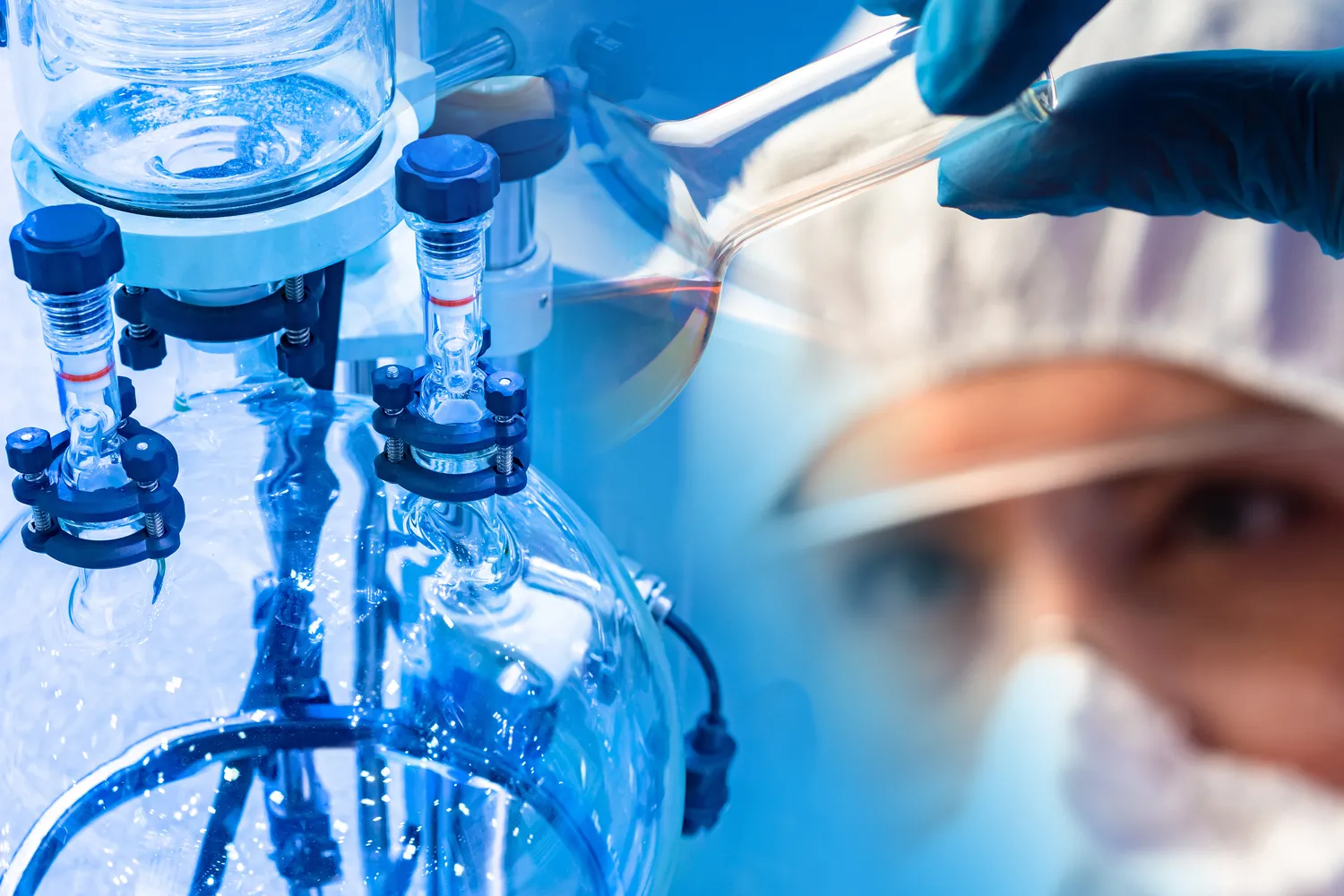
Destylarki do rozpuszczalników
Destylarki do rozpuszczalników znajdują szerokie zastosowanie w różnych dziedzinach przemysłu oraz nauki. Jednym z najważniejszych obszarów ich wykorzystania jest przemysł chemiczny, gdzie służą do oczyszczania surowców oraz produktów końcowych. Dzięki nim możliwe jest uzyskanie substancji o wysokiej czystości, co ma kluczowe znaczenie dla jakości finalnych produktów. W laboratoriach naukowych destylarki wykorzystywane są do analizy chemicznej oraz badań nad nowymi związkami chemicznymi. Kolejnym istotnym zastosowaniem jest przemysł farmaceutyczny, gdzie czystość substancji czynnych ma fundamentalne znaczenie dla bezpieczeństwa leków. Destylacja znajduje również zastosowanie w przemyśle spożywczym, na przykład przy produkcji alkoholi czy olejków eterycznych. W każdym z tych przypadków kluczowe jest dokładne monitorowanie procesu destylacji oraz kontrola warunków pracy urządzeń, aby zapewnić optymalne wyniki i minimalizować ryzyko zanieczyszczeń.
Jakie są różnice między różnymi typami destylarek do rozpuszczalników
Na rynku dostępnych jest wiele różnych typów destylarek do rozpuszczalników, które różnią się konstrukcją oraz przeznaczeniem. Jednym z najpopularniejszych modeli są destylarki prostokątne, które charakteryzują się prostą budową i łatwością obsługi. Są one idealne do podstawowych procesów destylacji i często stosowane w laboratoriach edukacyjnych lub mniejszych zakładach przemysłowych. Z kolei bardziej zaawansowane modele to destylarki kolumnowe, które umożliwiają przeprowadzanie skomplikowanych procesów destylacji frakcyjnej. Te urządzenia wyposażone są w kolumny separacyjne, które pozwalają na efektywne oddzielanie składników o różnych temperaturach wrzenia. Innym rodzajem są destylarki próżniowe, które działają w obniżonym ciśnieniu, co umożliwia destylację substancji o wysokiej temperaturze wrzenia bez ryzyka ich degradacji.
Jakie czynniki wpływają na wybór destylarki do rozpuszczalników
Wybór odpowiedniej destylarki do rozpuszczalników jest kluczowy dla efektywności procesów chemicznych oraz jakości uzyskiwanych produktów. Istnieje wiele czynników, które należy wziąć pod uwagę przy podejmowaniu decyzji. Przede wszystkim istotne jest określenie rodzaju substancji, które będą destylowane, ponieważ różne materiały wymagają różnych podejść technologicznych. Na przykład, jeśli planujemy destylować substancje o niskiej temperaturze wrzenia, warto rozważyć zakup destylarki próżniowej, która umożliwia przeprowadzanie procesów w obniżonym ciśnieniu. Kolejnym czynnikiem jest wydajność urządzenia – w przypadku dużych zakładów przemysłowych konieczne może być zainwestowanie w bardziej zaawansowane modele kolumnowe, które zapewniają wyższą efektywność separacji. Ważnym aspektem jest również łatwość obsługi i konserwacji destylarki. Warto zwrócić uwagę na to, czy urządzenie jest wyposażone w systemy automatyzacji, które mogą znacznie ułatwić pracę i zminimalizować ryzyko błędów.
Jakie są najnowsze technologie w dziedzinie destylacji rozpuszczalników
W ostatnich latach technologia destylacji rozpuszczalników znacznie się rozwijała, co przyczyniło się do powstania nowoczesnych rozwiązań zwiększających efektywność i bezpieczeństwo tych procesów. Jednym z najważniejszych trendów jest automatyzacja procesów destylacyjnych. Nowoczesne destylarki są często wyposażone w zaawansowane systemy monitorowania i kontroli, które pozwalają na precyzyjne zarządzanie parametrami pracy urządzenia. Dzięki temu możliwe jest uzyskanie stabilnych wyników oraz minimalizacja ryzyka wystąpienia błędów ludzkich. Innowacyjne rozwiązania obejmują także zastosowanie materiałów kompozytowych i nanotechnologii, które poprawiają wydajność wymiany ciepła oraz odporność na działanie agresywnych chemikaliów. Warto również zwrócić uwagę na rozwój technologii odzysku energii, która pozwala na zmniejszenie kosztów operacyjnych poprzez wykorzystanie ciepła odpadowego z procesów destylacji do podgrzewania innych mediów.
Jakie są najczęstsze błędy przy używaniu destylarek do rozpuszczalników
Użytkowanie destylarek do rozpuszczalników wiąże się z pewnymi ryzykami oraz wyzwaniami, które mogą prowadzić do niepożądanych efektów lub uszkodzeń sprzętu. Jednym z najczęstszych błędów jest niewłaściwe ustawienie parametrów pracy urządzenia, takich jak temperatura czy ciśnienie. Niezgodność tych wartości z wymaganiami procesu może prowadzić do niskiej wydajności destylacji lub nawet uszkodzenia substancji chemicznych. Kolejnym problemem jest brak regularnej konserwacji sprzętu – zaniedbanie tego aspektu może prowadzić do gromadzenia się osadów oraz korozji elementów konstrukcyjnych, co skraca żywotność urządzenia i wpływa na jakość uzyskiwanych produktów. Użytkownicy często pomijają również znaczenie odpowiedniego przygotowania materiału przed rozpoczęciem procesu destylacji. Zanieczyszczenia mechaniczne mogą wpłynąć na wyniki analizy oraz jakość końcowego produktu. Warto także pamiętać o bezpieczeństwie – nieprzestrzeganie zasad BHP podczas obsługi destylarek może prowadzić do poważnych wypadków.
Jakie są różnice między destylacją prostą a frakcyjną
Destylacja prosta i frakcyjna to dwa podstawowe rodzaje procesów stosowanych w destylarkach do rozpuszczalników, które różnią się zarówno metodą przeprowadzania procesu, jak i jego zastosowaniem. Destylacja prosta polega na jednorazowym podgrzewaniu cieczy i skraplaniu pary, co pozwala na oddzielanie substancji o znacznie różniących się temperaturach wrzenia. Jest to metoda stosunkowo prosta i szybka, idealna dla mieszanin zawierających jeden główny składnik oraz niewielką ilość zanieczyszczeń. Z kolei destylacja frakcyjna to bardziej skomplikowany proces, który wykorzystuje kolumny separacyjne do wielokrotnego podgrzewania i skraplania pary. Dzięki temu możliwe jest uzyskanie lepszej separacji składników o podobnych temperaturach wrzenia, co czyni tę metodę bardziej efektywną w przypadku skomplikowanych mieszanin chemicznych. Destylacja frakcyjna znajduje zastosowanie w przemyśle petrochemicznym oraz farmaceutycznym, gdzie wymagana jest wysoka czystość produktów końcowych.
Jakie są najlepsze praktyki dotyczące obsługi destylarek do rozpuszczalników
Aby zapewnić efektywne i bezpieczne użytkowanie destylarek do rozpuszczalników, warto przestrzegać kilku najlepszych praktyk dotyczących ich obsługi. Przede wszystkim kluczowe jest zapoznanie się z instrukcją obsługi dostarczoną przez producenta urządzenia – zawiera ona istotne informacje dotyczące parametrów pracy oraz zasad bezpieczeństwa. Regularne przeglądy techniczne są niezbędne dla utrzymania sprzętu w dobrym stanie – zaleca się kontrolowanie stanu uszczelek, rur oraz innych elementów konstrukcyjnych. Ważne jest również odpowiednie przygotowanie materiału przed rozpoczęciem procesu destylacji – wszelkie zanieczyszczenia mechaniczne powinny być usunięte, aby uniknąć problemów podczas analizy końcowej. Podczas pracy z substancjami chemicznymi należy zawsze stosować odpowiednie środki ochrony osobistej – rękawice, gogle ochronne oraz odzież robocza to podstawowe elementy wyposażenia każdego laboranta czy technika chemicznego.
Jakie są koszty zakupu i eksploatacji destylarek do rozpuszczalników
Koszty zakupu i eksploatacji destylarek do rozpuszczalników mogą się znacznie różnić w zależności od wielu czynników, takich jak typ urządzenia, jego wydajność oraz dodatkowe funkcje technologiczne. Na rynku dostępne są zarówno proste modele laboratoryjne, których ceny zaczynają się od kilku tysięcy złotych, jak i zaawansowane systemy przemysłowe kosztujące kilkaset tysięcy złotych lub więcej. Przy wyborze odpowiedniej destylarki warto uwzględnić nie tylko cenę zakupu, ale także koszty eksploatacji związane z energią elektryczną potrzebną do podgrzewania cieczy oraz ewentualnymi kosztami konserwacji i naprawy sprzętu. Dodatkowo należy brać pod uwagę koszty związane z zakupem materiałów eksploatacyjnych takich jak uszczelki czy filtry. W przypadku dużych zakładów przemysłowych warto również uwzględnić potencjalne oszczędności wynikające z efektywnego odzysku rozpuszczalników oraz minimalizacji odpadów chemicznych dzięki zastosowaniu nowoczesnych technologii destylacyjnych.