Destylacja rozpuszczalników to proces separacji substancji na podstawie różnicy ich temperatur wrzenia. Jest to jedna z najstarszych i najczęściej stosowanych metod oczyszczania cieczy, która znajduje zastosowanie w wielu dziedzinach, od przemysłu chemicznego po laboratoria badawcze. Proces ten polega na podgrzewaniu mieszaniny cieczy, co powoduje odparowanie składników o niższej temperaturze wrzenia. Opary te następnie są schładzane i kondensowane, tworząc czystą ciecz, która jest zbierana w osobnym naczyniu. Kluczowym elementem tego procesu jest kolumna destylacyjna, która zwiększa efektywność separacji poprzez wielokrotne skraplanie i odparowywanie. W zależności od zastosowania, destylacja może być przeprowadzana w różnych warunkach, takich jak destylacja prosta, frakcyjna czy próżniowa.
Jakie są zastosowania destylacji rozpuszczalników w przemyśle
Destylacja rozpuszczalników ma szerokie zastosowanie w różnych sektorach przemysłowych, w tym w produkcji chemikaliów, farmaceutyków oraz w przemyśle spożywczym. W przemyśle chemicznym proces ten jest kluczowy do oczyszczania surowców oraz produktów końcowych. Dzięki destylacji można uzyskać wysokiej czystości substancje chemiczne, które są niezbędne do produkcji farb, lakierów czy tworzyw sztucznych. W farmacji destylacja jest wykorzystywana do izolacji aktywnych składników leków oraz ich oczyszczania z zanieczyszczeń. W przemyśle spożywczym proces ten znajduje zastosowanie przy produkcji alkoholu oraz ekstraktów smakowych. Destylacja pozwala na uzyskanie pożądanych aromatów i smaków poprzez oddzielenie ich od niepożądanych substancji.
Jakie są różnice między destylacją prostą a frakcyjną
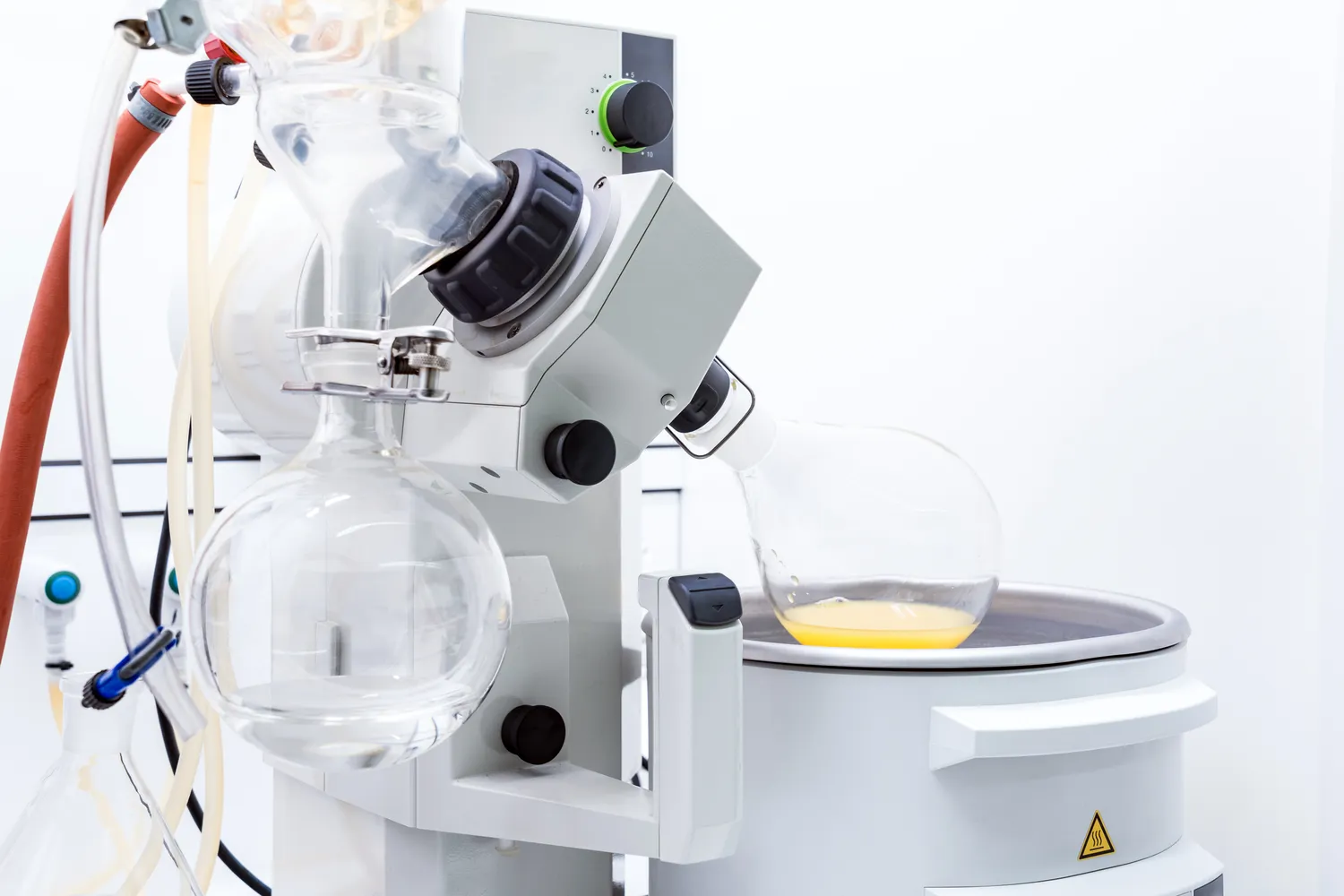
Destylacja rozpuszczalników
Destylacja prosta i frakcyjna to dwie podstawowe metody stosowane w procesie destylacji rozpuszczalników, które różnią się zarówno pod względem technologicznym, jak i efektywności separacji. Destylacja prosta polega na jednorazowym podgrzewaniu cieczy i zbieraniu oparów bez dodatkowych etapów separacji. Ta metoda sprawdza się najlepiej w przypadku mieszanin składających się z dwóch składników o znacznie różniących się temperaturach wrzenia. Natomiast destylacja frakcyjna jest bardziej skomplikowanym procesem, który wykorzystuje kolumnę destylacyjną do wielokrotnego skraplania i odparowywania oparów. Dzięki temu możliwe jest uzyskanie lepszej separacji składników o podobnych temperaturach wrzenia. Frakcyjna destylacja jest szczególnie przydatna w przypadku mieszanin zawierających wiele substancji chemicznych, gdzie precyzyjne oddzielenie poszczególnych komponentów jest kluczowe dla jakości końcowego produktu.
Jakie są zalety i ograniczenia destylacji rozpuszczalników
Destylacja rozpuszczalników ma wiele zalet, które przyczyniają się do jej popularności w różnych branżach przemysłowych. Przede wszystkim pozwala na uzyskanie wysokiej czystości substancji chemicznych oraz skuteczne usuwanie zanieczyszczeń. Proces ten jest również stosunkowo prosty do zautomatyzowania, co zwiększa jego efektywność i zmniejsza koszty operacyjne. Dodatkowo, destylacja może być dostosowywana do różnych rodzajów mieszanin oraz wymagań dotyczących czystości produktów końcowych. Jednakże istnieją również pewne ograniczenia związane z tą metodą. Przede wszystkim proces ten może być czasochłonny i wymaga dużej ilości energii, co wpływa na koszty produkcji. Ponadto nie wszystkie substancje mogą być skutecznie oddzielane za pomocą destylacji, zwłaszcza te o bliskich temperaturach wrzenia lub te, które ulegają rozkładowi podczas podgrzewania.
Jakie są najczęstsze błędy podczas destylacji rozpuszczalników
Podczas przeprowadzania procesu destylacji rozpuszczalników istnieje wiele pułapek, w które można wpaść, co może prowadzić do nieefektywności lub zanieczyszczenia końcowego produktu. Jednym z najczęstszych błędów jest niewłaściwe ustawienie temperatury podgrzewania. Zbyt wysoka temperatura może spowodować, że składniki o wyższej temperaturze wrzenia również odparują, co prowadzi do zanieczyszczenia destylatu. Z kolei zbyt niska temperatura może skutkować niepełnym odparowaniem substancji, co również wpływa na jakość uzyskanego produktu. Innym istotnym błędem jest niewłaściwe dobranie kolumny destylacyjnej. W przypadku mieszanin o bliskich temperaturach wrzenia, kolumna o niewłaściwej wysokości lub liczbie teoretycznych półek może znacząco obniżyć efektywność separacji. Ponadto, brak odpowiedniego chłodzenia kondensatora może prowadzić do utraty części destylatu w postaci pary. Należy również pamiętać o regularnym czyszczeniu sprzętu, ponieważ resztki poprzednich procesów mogą zanieczyścić nowo destylowane substancje.
Jakie są różnice między destylacją a innymi metodami separacji
Destylacja rozpuszczalników to jedna z wielu metod separacji substancji chemicznych, ale różni się od innych technik, takich jak ekstrakcja czy chromatografia. Główna różnica polega na zasadzie działania – destylacja opiera się na różnicy temperatur wrzenia składników, podczas gdy ekstrakcja wykorzystuje różnice w rozpuszczalności substancji w różnych rozpuszczalnikach. Ekstrakcja może być bardziej efektywna w przypadku substancji, które mają podobne temperatury wrzenia, ale różnią się rozpuszczalnością. Z kolei chromatografia to technika separacji oparta na interakcji pomiędzy składnikami a materiałem stacjonarnym, co pozwala na uzyskanie bardzo wysokiej czystości produktów. Choć każda z tych metod ma swoje zalety i ograniczenia, wybór odpowiedniej techniki zależy od specyfiki danej aplikacji oraz wymagań dotyczących czystości i wydajności procesu.
Jakie są nowoczesne technologie związane z destylacją rozpuszczalników
W ostatnich latach rozwój technologii związanych z destylacją rozpuszczalników przyniósł wiele innowacji, które zwiększają efektywność i oszczędność tego procesu. Jednym z najważniejszych osiągnięć jest zastosowanie technologii membranowych, które umożliwiają separację substancji bez konieczności podgrzewania ich do wysokich temperatur. Dzięki temu można zaoszczędzić energię oraz zmniejszyć ryzyko degradacji termicznej składników. Innowacyjne systemy automatyzacji i monitorowania procesów destylacyjnych pozwalają na precyzyjne kontrolowanie warunków pracy oraz szybką reakcję na zmiany w składzie mieszaniny. Dodatkowo, rozwój materiałów o wysokiej wydajności dla kolumn destylacyjnych przyczynia się do poprawy efektywności separacji oraz redukcji strat surowców. Coraz częściej wykorzystywane są także technologie odzysku ciepła, które pozwalają na ponowne wykorzystanie energii cieplnej generowanej podczas procesu destylacji.
Jakie są wymagania dotyczące bezpieczeństwa podczas destylacji
Bezpieczeństwo podczas przeprowadzania procesu destylacji rozpuszczalników jest kluczowym aspektem, który należy uwzględnić na każdym etapie pracy. Przede wszystkim ważne jest zapewnienie odpowiedniej wentylacji w pomieszczeniu, gdzie odbywa się proces, aby uniknąć gromadzenia się szkodliwych oparów chemicznych. Użytkownicy powinni nosić odpowiednie środki ochrony osobistej, takie jak rękawice i okulary ochronne, aby zminimalizować ryzyko kontaktu ze szkodliwymi substancjami. Należy również pamiętać o tym, że wiele rozpuszczalników jest łatwopalnych, dlatego ważne jest unikanie otwartego ognia oraz źródeł zapłonu w pobliżu urządzeń destylacyjnych. Regularne kontrole sprzętu oraz konserwacja instalacji są niezbędne do zapewnienia ich sprawności i bezpieczeństwa użytkowania. Ponadto warto przeprowadzać szkolenia dla pracowników dotyczące procedur awaryjnych oraz postępowania w przypadku wystąpienia niebezpiecznych sytuacji.
Jakie są przyszłe kierunki badań nad destylacją rozpuszczalników
Przyszłość badań nad destylacją rozpuszczalników koncentruje się na poszukiwaniu bardziej efektywnych i ekologicznych metod separacji substancji chemicznych. W obliczu rosnących wymagań dotyczących ochrony środowiska i zrównoważonego rozwoju naukowcy skupiają się na opracowywaniu nowych technologii, które pozwolą na zmniejszenie zużycia energii oraz emisji szkodliwych substancji do atmosfery. Badania nad zastosowaniem nanomateriałów w kolumnach destylacyjnych mogą przyczynić się do poprawy efektywności separacji poprzez zwiększenie powierzchni kontaktu między fazami ciekłą a gazową. Również rozwój biotechnologii i enzymatycznych procesów separacyjnych staje się coraz bardziej popularny jako alternatywa dla tradycyjnej destylacji. W przyszłości możemy spodziewać się także większego wykorzystania sztucznej inteligencji oraz algorytmów optymalizacji w projektowaniu procesów destylacyjnych, co pozwoli na lepsze dostosowanie warunków pracy do specyfiki danej mieszaniny chemicznej.
Jakie są różnice w kosztach między różnymi metodami destylacji
Koszty związane z procesem destylacji rozpuszczalników mogą się znacznie różnić w zależności od zastosowanej metody oraz skali produkcji. Destylacja prosta, będąca najłatwiejszą formą tego procesu, zazwyczaj wiąże się z niższymi kosztami operacyjnymi, jednak jej efektywność jest ograniczona do mieszanin o wyraźnie różniących się temperaturach wrzenia. W przypadku bardziej złożonych mieszanin, gdzie wymagane jest uzyskanie wysokiej czystości produktów, destylacja frakcyjna staje się bardziej opłacalna mimo wyższych kosztów początkowych związanych z zakupem i eksploatacją kolumny destylacyjnej. Dodatkowo, nowoczesne technologie, takie jak destylacja próżniowa czy membranowa, mogą generować wyższe koszty inwestycyjne, ale w dłuższym okresie mogą przynieść oszczędności dzięki zmniejszeniu zużycia energii oraz lepszej wydajności separacji.
Jakie są kluczowe czynniki wpływające na efektywność destylacji
Efektywność procesu destylacji rozpuszczalników zależy od wielu czynników, które należy starannie kontrolować i optymalizować. Jednym z najważniejszych aspektów jest temperatura podgrzewania, która musi być dostosowana do specyfiki danej mieszaniny chemicznej. Zbyt wysoka temperatura może prowadzić do niepożądanych reakcji chemicznych oraz zanieczyszczenia produktu końcowego. Kolejnym kluczowym czynnikiem jest ciśnienie, które ma istotny wpływ na temperatury wrzenia składników. W przypadku destylacji próżniowej obniżenie ciśnienia pozwala na przeprowadzenie procesu w niższych temperaturach, co jest korzystne dla substancji wrażliwych na ciepło. Ponadto konstrukcja kolumny destylacyjnej oraz wybór odpowiednich materiałów mają znaczenie dla efektywności separacji. Wysokość kolumny oraz liczba teoretycznych półek powinny być dostosowane do charakterystyki mieszaniny.