Kompresor to urządzenie mechaniczne, którego głównym zadaniem jest zwiększenie ciśnienia gazu poprzez zmniejszenie jego objętości. W praktyce oznacza to, że kompresory są wykorzystywane w różnych dziedzinach przemysłu oraz w codziennym życiu, gdzie potrzebne jest sprężone powietrze lub inne gazy. Działanie kompresora opiera się na zasadzie termodynamiki, a jego konstrukcja może być różnorodna, w zależności od zastosowania. Najpopularniejsze typy kompresorów to kompresory tłokowe, śrubowe oraz rotacyjne. Kompresory tłokowe działają na zasadzie ruchu posuwistego tłoka, który spręża gaz w cylindrze, podczas gdy kompresory śrubowe wykorzystują obracające się wirniki do sprężania gazu. Kompresory rotacyjne z kolei charakteryzują się ciągłym przepływem gazu przez wirujące elementy.
Jakie są zastosowania kompresorów w przemyśle?
Kompresory znajdują szerokie zastosowanie w różnych sektorach przemysłu, co czyni je niezwykle wszechstronnymi urządzeniami. W przemyśle budowlanym kompresory są używane do zasilania narzędzi pneumatycznych, takich jak młoty udarowe czy wiertarki. Dzięki sprężonemu powietrzu możliwe jest efektywne wykonywanie prac budowlanych oraz remontowych. W przemyśle motoryzacyjnym kompresory służą do pompowania opon oraz zasilania systemów klimatyzacji. W zakładach produkcyjnych kompresory są wykorzystywane do transportu materiałów sypkich oraz w procesach technologicznych wymagających sprężonego powietrza. Dodatkowo, w branży spożywczej kompresory odgrywają kluczową rolę w pakowaniu produktów oraz ich konserwacji. Warto również wspomnieć o zastosowaniach medycznych, gdzie sprężone powietrze jest niezbędne do działania sprzętu medycznego, takiego jak respiratory czy inhalatory.
Jakie są różnice między różnymi typami kompresorów?
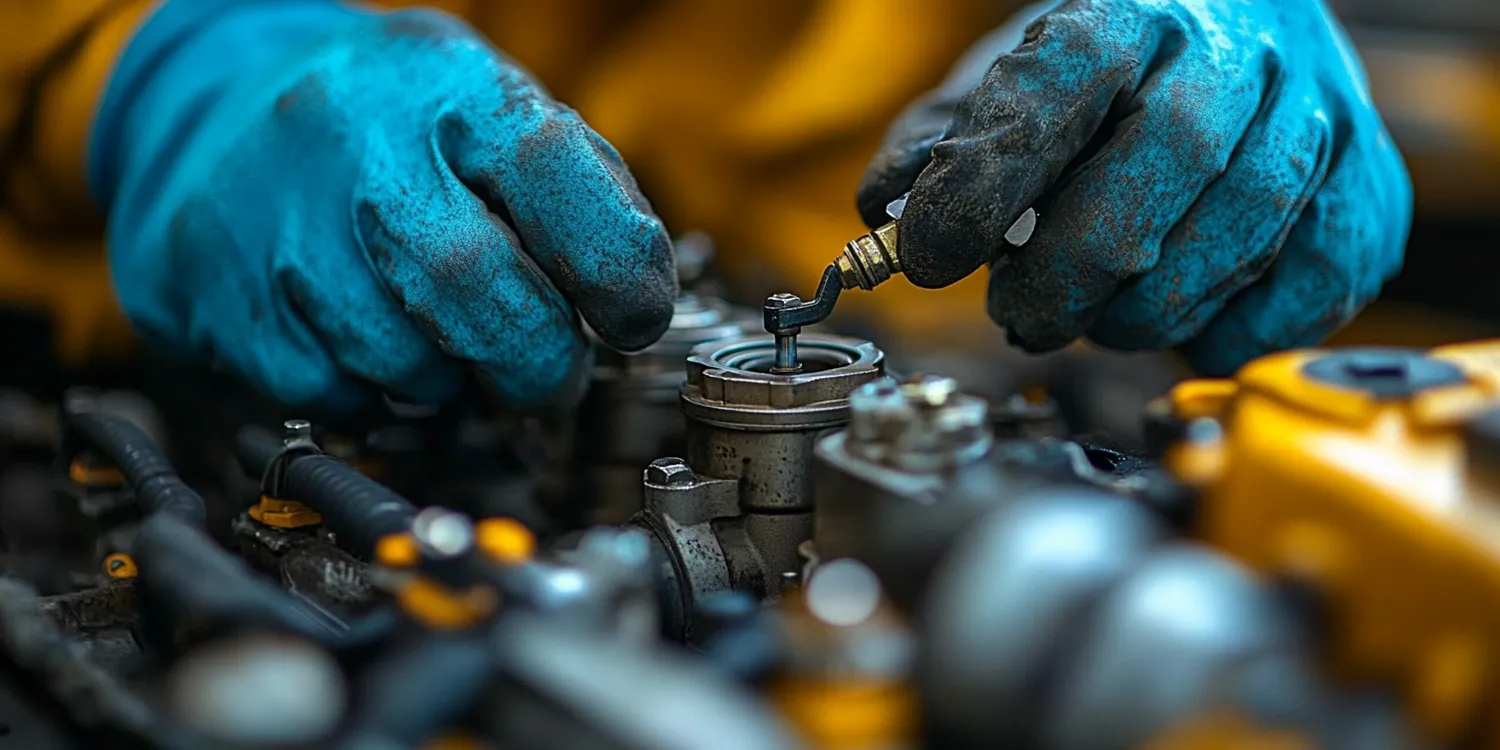
Kompresory co to jest?
Wybór odpowiedniego typu kompresora jest kluczowy dla efektywności jego działania oraz dostosowania do konkretnych potrzeb użytkownika. Kompresory tłokowe charakteryzują się prostą konstrukcją i stosunkowo niskimi kosztami zakupu, jednak ich wydajność może być ograniczona przy długotrwałym użytkowaniu. Z kolei kompresory śrubowe oferują wyższą wydajność oraz mniejsze zużycie energii, co czyni je idealnym rozwiązaniem dla dużych zakładów produkcyjnych wymagających ciągłego dostępu do sprężonego powietrza. Kompresory rotacyjne są natomiast znane z cichej pracy i kompaktowych rozmiarów, co sprawia, że doskonale sprawdzają się w miejscach o ograniczonej przestrzeni. Ważnym aspektem przy wyborze kompresora jest również jego moc oraz ciśnienie robocze, które powinny być dostosowane do specyfiki wykonywanych prac.
Jakie są koszty zakupu i eksploatacji kompresora?
Koszty związane z zakupem i eksploatacją kompresora mogą się znacznie różnić w zależności od jego typu oraz przeznaczenia. Na rynku dostępne są zarówno tanie modele kompresorów tłokowych, które można nabyć za kilka tysięcy złotych, jak i droższe urządzenia śrubowe czy rotacyjne, których ceny mogą sięgać kilkudziesięciu tysięcy złotych. Oprócz kosztu zakupu warto również uwzględnić wydatki związane z eksploatacją urządzenia, takie jak koszty energii elektrycznej potrzebnej do jego działania oraz regularne serwisowanie i konserwację. W przypadku intensywnego użytkowania kompresora istotne będą także koszty wymiany części eksploatacyjnych, takich jak filtry czy oleje smarowe. Warto zwrócić uwagę na parametry energetyczne urządzenia, ponieważ bardziej efektywne modele mogą znacząco obniżyć koszty eksploatacji w dłuższym okresie czasu.
Jakie są najczęstsze problemy z kompresorami?
Kompresory, jak każde urządzenia mechaniczne, mogą napotykać różne problemy w trakcie swojej pracy. Jednym z najczęstszych problemów jest niewłaściwe smarowanie, które może prowadzić do nadmiernego zużycia części oraz awarii. W przypadku kompresorów tłokowych, brak odpowiedniego oleju smarowego może spowodować zatarcie się tłoka, co skutkuje kosztowną naprawą lub koniecznością wymiany całego urządzenia. Innym częstym problemem jest nieszczelność układu sprężonego powietrza, co prowadzi do utraty ciśnienia i obniżenia wydajności kompresora. Nieszczelności mogą występować w wężach, złączkach lub samym zbiorniku sprężonego powietrza. Regularne kontrole i konserwacja są kluczowe dla zapobiegania tego typu problemom. Ponadto, kompresory mogą również borykać się z problemami związanymi z przegrzewaniem się silnika, co często jest wynikiem zbyt długiej pracy bez przerwy lub niewłaściwego chłodzenia.
Jakie są zalety korzystania z kompresora?
Korzystanie z kompresora niesie ze sobą wiele korzyści, zarówno w kontekście przemysłowym, jak i domowym. Przede wszystkim, sprężone powietrze generowane przez kompresor jest niezwykle wszechstronne i może być wykorzystywane do różnych zastosowań. Dzięki temu można zaoszczędzić czas i pieniądze, inwestując w jedno urządzenie zamiast wielu różnych narzędzi. Kompresory umożliwiają efektywne zasilanie narzędzi pneumatycznych, co zwiększa ich wydajność oraz precyzję pracy. Dodatkowo, sprężone powietrze jest czystsze niż inne źródła energii, takie jak paliwa kopalne, co przyczynia się do zmniejszenia emisji szkodliwych substancji do atmosfery. Kompresory są także stosunkowo łatwe w obsłudze i konserwacji, co sprawia, że nawet osoby bez specjalistycznej wiedzy mogą je użytkować.
Jakie są różnice między kompresorami stacjonarnymi a przenośnymi?
Kiedy decydujemy się na zakup kompresora, jednym z kluczowych aspektów do rozważenia jest wybór między modelem stacjonarnym a przenośnym. Kompresory stacjonarne zazwyczaj charakteryzują się większą mocą oraz pojemnością zbiornika na sprężone powietrze, co sprawia, że są idealnym rozwiązaniem dla dużych zakładów przemysłowych czy warsztatów wymagających ciągłego dostępu do sprężonego powietrza. Ich konstrukcja pozwala na długotrwałą pracę bez konieczności częstego uzupełniania zbiornika. Z drugiej strony, kompresory przenośne są znacznie bardziej mobilne i łatwiejsze w transporcie, co czyni je doskonałym wyborem dla osób wykonujących prace w różnych lokalizacjach. Często mają mniejszą moc i pojemność zbiornika, ale ich zaletą jest możliwość łatwego przewożenia oraz użytkowania w terenie. Wybór pomiędzy tymi dwoma typami zależy od specyfiki wykonywanych prac oraz indywidualnych potrzeb użytkownika.
Jakie cechy powinien mieć dobry kompresor?
Wybierając kompresor, warto zwrócić uwagę na kilka kluczowych cech, które mogą znacząco wpłynąć na jego wydajność oraz komfort użytkowania. Przede wszystkim istotna jest moc silnika oraz wydajność sprężania, które powinny być dostosowane do specyficznych potrzeb użytkownika. Ważnym parametrem jest również pojemność zbiornika na sprężone powietrze – im większy zbiornik, tym dłużej można korzystać z narzędzi pneumatycznych bez konieczności przerywania pracy na uzupełnienie powietrza. Kolejnym aspektem jest poziom hałasu generowanego przez kompresor; cichsze modele będą bardziej komfortowe w użytkowaniu, zwłaszcza w zamkniętych pomieszczeniach. Dobry kompresor powinien także być wyposażony w system filtracji powietrza oraz zabezpieczenia przed przegrzewaniem się silnika.
Jakie są nowoczesne technologie stosowane w kompresorach?
Nowoczesne technologie stosowane w kompresorach znacząco poprawiają ich wydajność oraz efektywność energetyczną. W ostatnich latach wiele modeli zostało wyposażonych w zaawansowane systemy zarządzania pracą silnika oraz automatyczne sterowanie ciśnieniem sprężonego powietrza. Dzięki tym rozwiązaniom możliwe jest optymalne dopasowanie pracy kompresora do aktualnych potrzeb użytkownika, co przekłada się na oszczędności energii oraz zmniejszenie kosztów eksploatacji. Innowacyjne technologie obejmują także zastosowanie materiałów o wysokiej odporności na zużycie oraz korozję, co zwiększa trwałość urządzeń i minimalizuje konieczność ich serwisowania. Dodatkowo niektóre nowoczesne modele wyposażone są w inteligentne systemy monitorowania pracy urządzenia za pomocą aplikacji mobilnych lub interfejsów internetowych, co pozwala na bieżąco kontrolować parametry pracy oraz diagnozować ewentualne problemy.
Jak dbać o kompresor aby służył przez lata?
Aby kompresor służył przez wiele lat bezawaryjnie, niezwykle istotna jest regularna konserwacja oraz przestrzeganie zasad jego użytkowania. Kluczowym elementem dbania o urządzenie jest regularna wymiana oleju smarowego zgodnie z zaleceniami producenta; odpowiedni poziom oleju zapewnia prawidłowe smarowanie ruchomych części i minimalizuje ryzyko ich uszkodzenia. Ważne jest również czyszczenie filtrów powietrza i wymiana wkładów filtracyjnych; brudne filtry mogą prowadzić do obniżenia wydajności oraz zwiększonego zużycia energii. Należy także regularnie sprawdzać stan przewodów i złączek pod kątem nieszczelności; wszelkie wycieki należy natychmiast naprawić, aby uniknąć strat ciśnienia sprężonego powietrza. Ponadto warto zadbać o odpowiednią wentylację wokół kompresora; przegrzewanie się urządzenia może prowadzić do jego uszkodzenia lub skrócenia żywotności silnika.
Jakie są najnowsze trendy w branży kompresorów?
W ostatnich latach branża kompresorów przechodzi dynamiczne zmiany, które są odpowiedzią na rosnące potrzeby użytkowników oraz wymagania dotyczące ochrony środowiska. Jednym z najważniejszych trendów jest rozwój technologii bezolejowych, które eliminują potrzebę stosowania oleju smarowego, co przekłada się na czystsze powietrze oraz mniejsze koszty eksploatacji. Wzrost zainteresowania energią odnawialną sprawia, że coraz więcej producentów wprowadza kompresory zasilane energią słoneczną lub innymi ekologicznymi źródłami energii. Dodatkowo, automatyzacja procesów oraz integracja z systemami zarządzania produkcją stają się standardem w nowoczesnych zakładach przemysłowych. Dzięki tym rozwiązaniom możliwe jest efektywne monitorowanie i optymalizacja pracy kompresorów, co prowadzi do oszczędności oraz zwiększenia wydajności produkcji. Warto również zauważyć rosnącą popularność kompresorów mobilnych, które umożliwiają pracę w terenie i są dostosowane do różnorodnych warunków atmosferycznych.